Unlocking Efficiency in Your Business with Machine Label Applicators
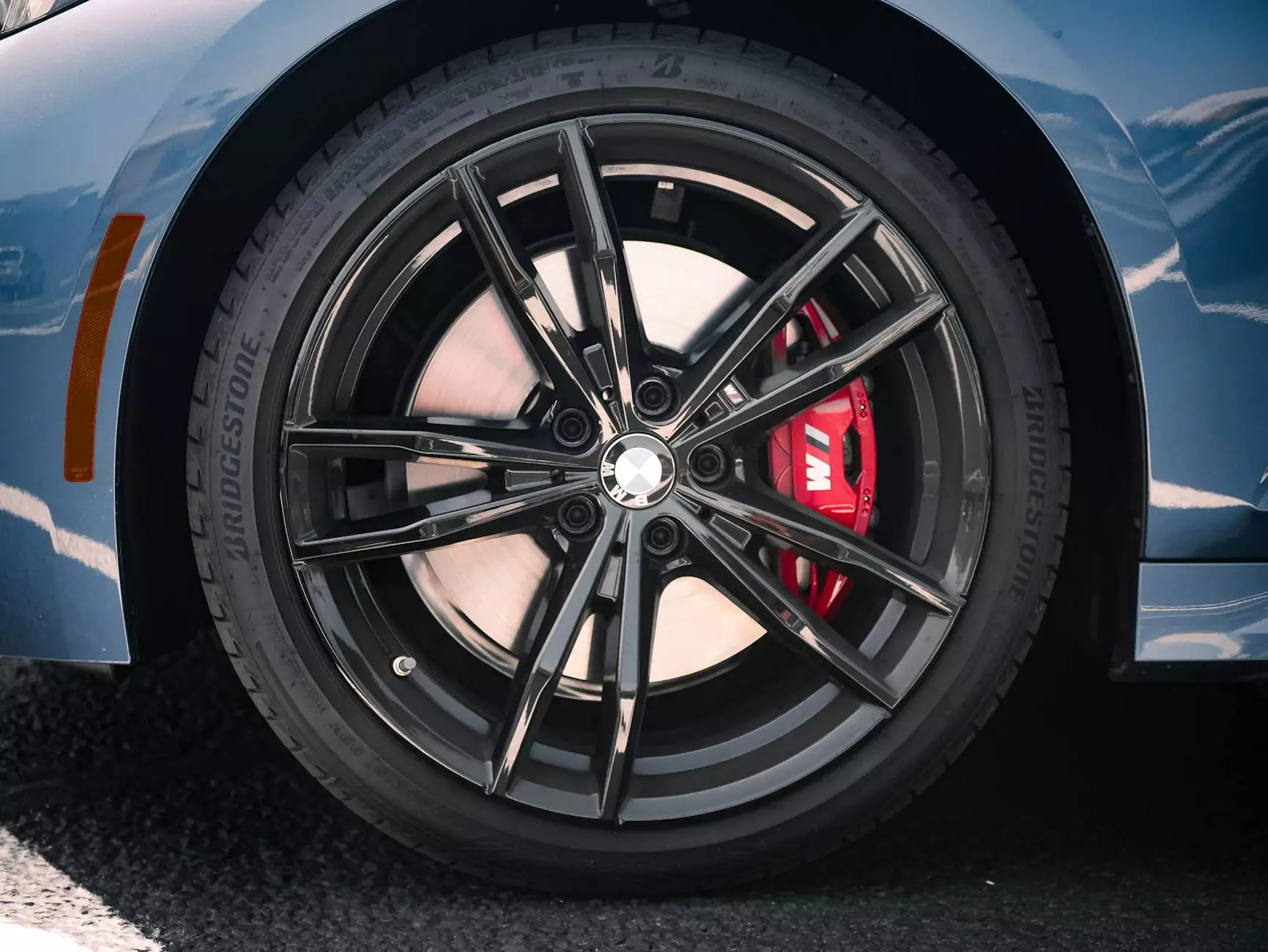
In today's fast-paced business environment, efficiency is key. For companies across various sectors, including printing services, electronics, and computers, leveraging technology to enhance operations is more crucial than ever. One such technology that has proven to be invaluable is the machine label applicator. This article delves deep into the benefits, functionality, and significance of these advanced devices, showcasing why your business should consider investing in them.
Understanding the Machine Label Applicator
A machine label applicator is a sophisticated device designed to automate the labeling process of products, packages, and various materials. It ensures that labels are applied precisely and consistently, alleviating the need for manual labeling which can be time-consuming and error-prone. By utilizing a machine label applicator, businesses can enhance their operational efficiency and significantly reduce labor costs.
Types of Machine Label Applicators
There are several types of machine label applicators, each tailored to meet specific requirements. Here are the most common:
- Pressure-Sensitive Label Applicators: These applicators use adhesives that activate under pressure, making them ideal for a variety of surfaces.
- Heat-Shrink Label Applicators: Used primarily in the beverage and food industries, these machines apply labels that shrink to fit the product once heated.
- Wrap-Around Label Applicators: Perfect for cylindrical products like bottles, these applicators wrap the label around the item for a seamless look.
- Top-Apply Label Applicators: These machines precisely place labels on the top side of products, common in packaging processes.
- Automatic Labeling Machines: These highly efficient machines can label various products at an astonishing speed, making them suitable for high-volume operations.
Advantages of Investing in a Machine Label Applicator
Investing in a machine label applicator offers numerous advantages that can lead to improved operations and increased profit margins. Here are some significant benefits:
1. Enhanced Productivity
With a machine label applicator, the speed at which products are labeled is significantly increased compared to manual labor. This automation allows businesses to scale their operations without the need for proportional increases in labor costs.
2. Consistency and Accuracy
One of the most significant downsides of manual labeling is the potential for human error. Automated labeling ensures that every label is applied uniformly, maintaining brand integrity and reducing waste due to mislabeling.
3. Cost Efficiency
Although there is an initial investment in a machine label applicator, the long-term savings in labor costs and the reduction in waste often result in a quick return on investment. Moreover, fewer errors mean lower costs associated with product recalls and reprints.
4. Improved Safety
Manual labeling can involve various safety hazards, especially in high-volume environments with moving parts. By automating this process, businesses can minimize workplace injuries related to label application.
5. Versatility
Modern machine label applicators are designed to handle a wide range of products and surfaces. This versatility means businesses can adapt their labeling processes without needing to invest in multiple types of equipment.
Choosing the Right Machine Label Applicator
When selecting a machine label applicator, it's essential to consider several factors to ensure the chosen model meets your business requirements:
1. Label Type and Size
Consider the types of labels you will use and their dimensions. Ensure that the applicator can handle these specifications effectively.
2. Product Type
Different products require different labeling techniques. Determine the types of products you’ll be labeling and choose an applicator suited for those shapes and sizes.
3. Speed Requirements
Evaluate your production speed. A high-speed production line will require a more robust labeling solution than a low-volume operation.
4. Ease of Use and Maintenance
Opt for a label applicator that is user-friendly and requires minimal maintenance to ensure continuous operation without significant downtime.
5. Budget Considerations
Determine your budget before exploring options. While more advanced machines may have a higher upfront cost, consider their long-term savings and benefits.
Case Studies: Success Stories with Machine Label Applicators
Many companies have experienced transformational changes in their operations with the use of machine label applicators. Here are a couple of case studies illustrating the impact:
Case Study 1: A Beverage Company
A mid-sized beverage company struggling with inefficiencies in their production line invested in a automated labeling system. After the installation of a machine label applicator, they reported an increase in labeling speed by over 300%, enabling them to boost production rates significantly. Furthermore, the accuracy of label placement reduced their waste and rework costs by 20% within the first quarter of operation.
Case Study 2: Electronics Manufacturer
An electronics manufacturer faced challenges with the variability of label application leading to inconsistencies in product branding. By switching to a high-precision machine label applicator, they achieved uniformity that not only enhanced their brand image but also increased customer satisfaction rates by 15% due to fewer labeling errors.
Maintaining Your Machine Label Applicator
To maximize the lifespan and efficiency of your machine label applicator, regular maintenance is crucial. Here are some essential tips:
- Regular Cleaning: Ensure that the machine is cleaned after each use to prevent residue buildup that can affect performance.
- Check Alignment: Regularly verify that the labeling mechanism is properly aligned to maintain accuracy.
- Inspect Components: Periodically check for any wear and tear on components, replacing them as needed to prevent breakdowns.
- Software Updates: If your applicator has software controls, ensure to keep them updated for optimal performance.
- Consult Manufacturer Guidelines: Always refer to the manufacturer’s maintenance guidelines for specific recommendations regarding your model.
Conclusion
In conclusion, adopting a machine label applicator in your business operations—be it in printing services, electronics, or computers—can lead to remarkable benefits, including enhanced productivity, improved accuracy, and significant cost savings. By understanding the types of applicators available and how to effectively choose and maintain them, your business can unlock new levels of efficiency, allowing you to focus on growth and innovation.
For companies looking to boost their operations, explore the variety of machine label applicators available and consider reaching out to experts at omegabrand.com for tailored solutions specific to your business needs.