The Essential Role of Precision Plastic Molds in Modern Manufacturing
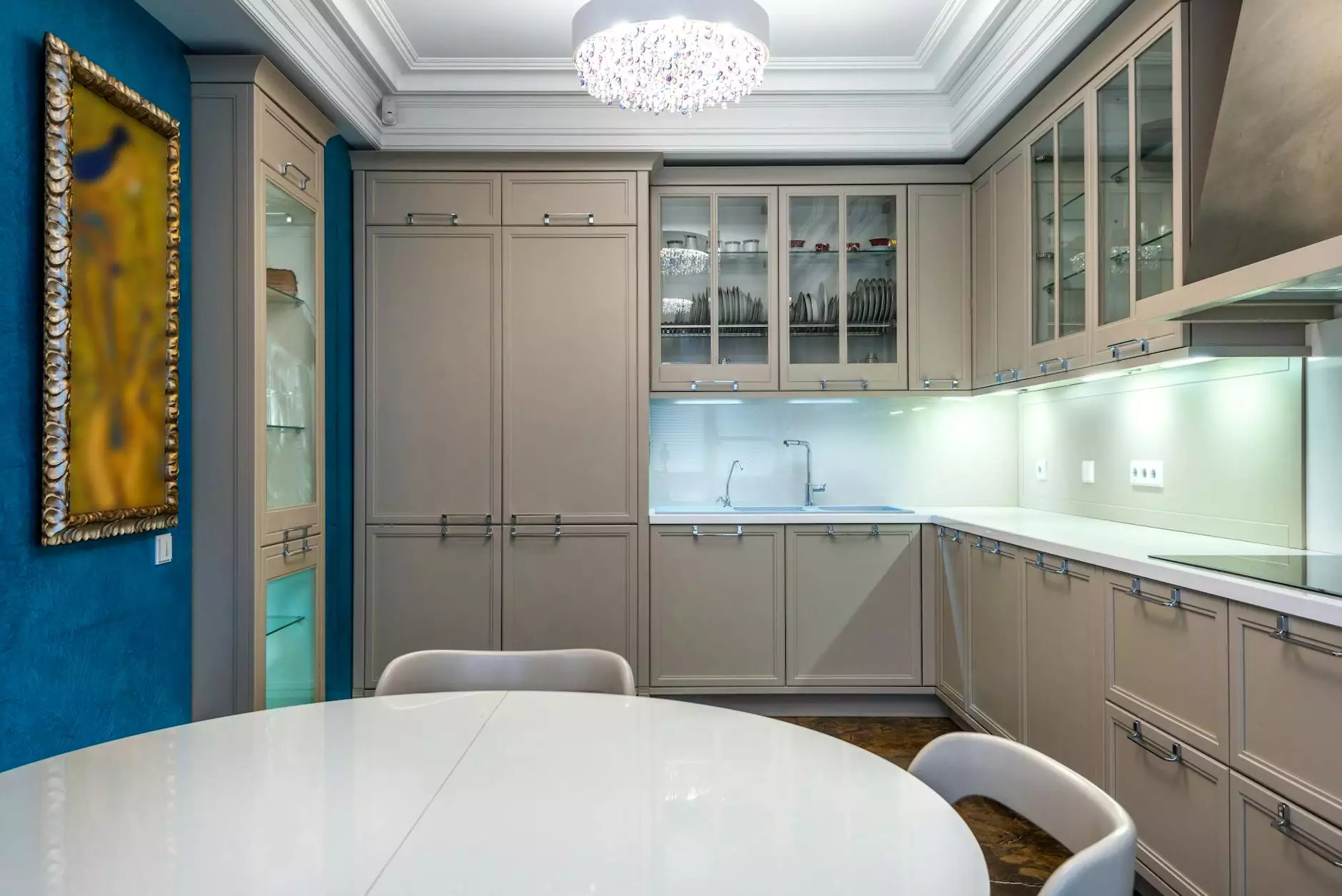
In the ever-evolving landscape of manufacturing, tools and techniques play a pivotal role in determining the quality, efficiency, and cost-effectiveness of production. One such important tool is the precision plastic mold. It is an indispensable component for industries ranging from automotive to consumer goods, pharmaceuticals, and electronics. This article explores the significance, design, manufacturing process, applications, and benefits of precision plastic molds, helping businesses understand their impact on manufacturing excellence.
Understanding Precision Plastic Molds
Precision plastic molds are engineered components used to shape liquid plastic into various forms. These molds are designed with exact specifications to ensure that every produced part meets stringent quality standards. The precision involved in the mold-making process is vital, as it directly affects the final product's performance and visual appeal.
The Importance of Precision in Mold Making
Precision in mold design and manufacturing is crucial for several reasons:
- Quality Control: High precision ensures minimal tolerances, reducing defects in produced parts.
- Cost Efficiency: Accurate molds reduce waste and ensure materials are used optimally.
- Improved Durability: Well-designed molds can withstand the pressure and heat involved in the injection molding process, enhancing their longevity.
- Enhanced Performance: Precise molds contribute to better-fitting parts, ensuring optimal performance in applications.
The Design Process of Precision Plastic Molds
The journey of creating a precision plastic mold begins with careful design considerations. Key aspects of the design process include:
1. Concept Development
Initially, the concept is developed through collaboration between designers and engineers. They consider the intended use of the molded part and begin drafting initial designs.
2. CAD Modeling
Advanced Computer-Aided Design (CAD) software is employed to create a 3D model of the mold. This step allows for precision adjustments and simulations of the molding process, ensuring all specifications are met before physical production begins.
3. Prototyping
A prototype of the mold can be created using techniques such as 3D printing. This allows for testing and modifications, ensuring the final design is optimized for production.
Manufacturing Process of Precision Plastic Molds
The manufacturing of precision plastic molds combines traditional craftsmanship with advanced technology. The key steps include:
1. Material Selection
Choosing the right materials for the mold is critical. Common materials include steel and aluminum, each offering unique benefits in terms of durability and heat resistance.
2. Machining
High-precision machining techniques, such as CNC machining, are employed to create the mold. These machines can operate with incredible accuracy, ensuring that every detail is reflected in the final product.
3. Finishing
The finishing process includes polishing and applying coatings to enhance the surface quality of the mold. This step is essential to prevent defects in the molded parts.
4. Assembly and Testing
Once the mold sections are machined and finished, they are assembled. Rigorous testing is conducted to ensure the mold functions correctly and produces parts within the required specifications.
Applications of Precision Plastic Molds
Precision plastic molds are utilized across various industries, showcasing their versatility. Some of the primary applications include:
1. Automotive Industry
The automotive sector uses precision molds to produce components such as dashboards, bumpers, and interior elements. The durability and aesthetic appeal of these parts are vital for vehicle performance and consumer satisfaction.
2. Consumer Goods
From toys to kitchenware, the demand for high-quality consumer goods drives the use of precision molds. These products require intricate designs and reliable performance, making precision molds essential.
3. Electronics
The electronics industry depends on precision molds to manufacture housings and components for devices like smartphones and computers. The need to precisely fit various electronic parts makes precision molding crucial.
4. Medical Technologies
In the medical field, precision molds are used to create devices that meet the highest hygiene and reliability standards. Components like syringes and surgical instruments must meet strict regulatory guidelines, reinforcing the importance of precision.
Benefits of Using Precision Plastic Molds
The adoption of precision plastic molds offers numerous advantages that enhance production processes, including:
1. Increased Productivity
By streamlining the molding process, precision molds facilitate faster production rates. This increase in productivity is accompanied by a decrease in cycle time, allowing more products to be manufactured within a shorter timeframe.
2. Cost Savings
While the initial investment in precision molds may be significant, the long-term cost savings from reduced material waste and lower labor costs often outweigh the initial expenditure.
3. Consistent Quality
The consistent manufacturing quality assured by precision molds leads to greater customer satisfaction and fewer returns. This is particularly crucial in industries where product quality is directly tied to brand reputation.
4. Customization and Versatility
Precision molds can be easily modified to accommodate varying designs and specifications, offering manufacturers the flexibility to adapt to market demands swiftly.
Choosing the Right Precision Mold Manufacturer
- Experience: Look for manufacturers with a proven track record in producing precision molds for your specific industry.
- Technology: Ensure they utilize the latest technology and methodologies in mold-making processes.
- Quality Assurance: A robust quality assurance process is critical for achieving the high standards expected in precision molding.
- Customer Support: Choose a manufacturer who values ongoing customer support and collaboration throughout the process.
The Future of Precision Plastic Molds
As technology progresses, the landscape of precision plastic molding continues to evolve. Innovations in materials science, such as bioplastics and advanced thermoplastics, are anticipated to play a significant role in shaping the future. Furthermore, Industry 4.0 technologies, including IoT and AI, are poised to enhance precision in mold-making, provide predictive maintenance, and improve overall production efficiency.
Conclusion
Precision plastic molds have undeniably transformed modern manufacturing by combining quality, versatility, and efficiency. As industries strive for better performance, embracing precision molding technology not only ensures better products but also serves as a competitive advantage. For businesses looking to innovate and excel, partnering with a reputable manufacturer like DeepMould can lead to remarkable enhancements in production capabilities and business growth.