Understanding 100i: The Future of Cutting and Welding Equipment
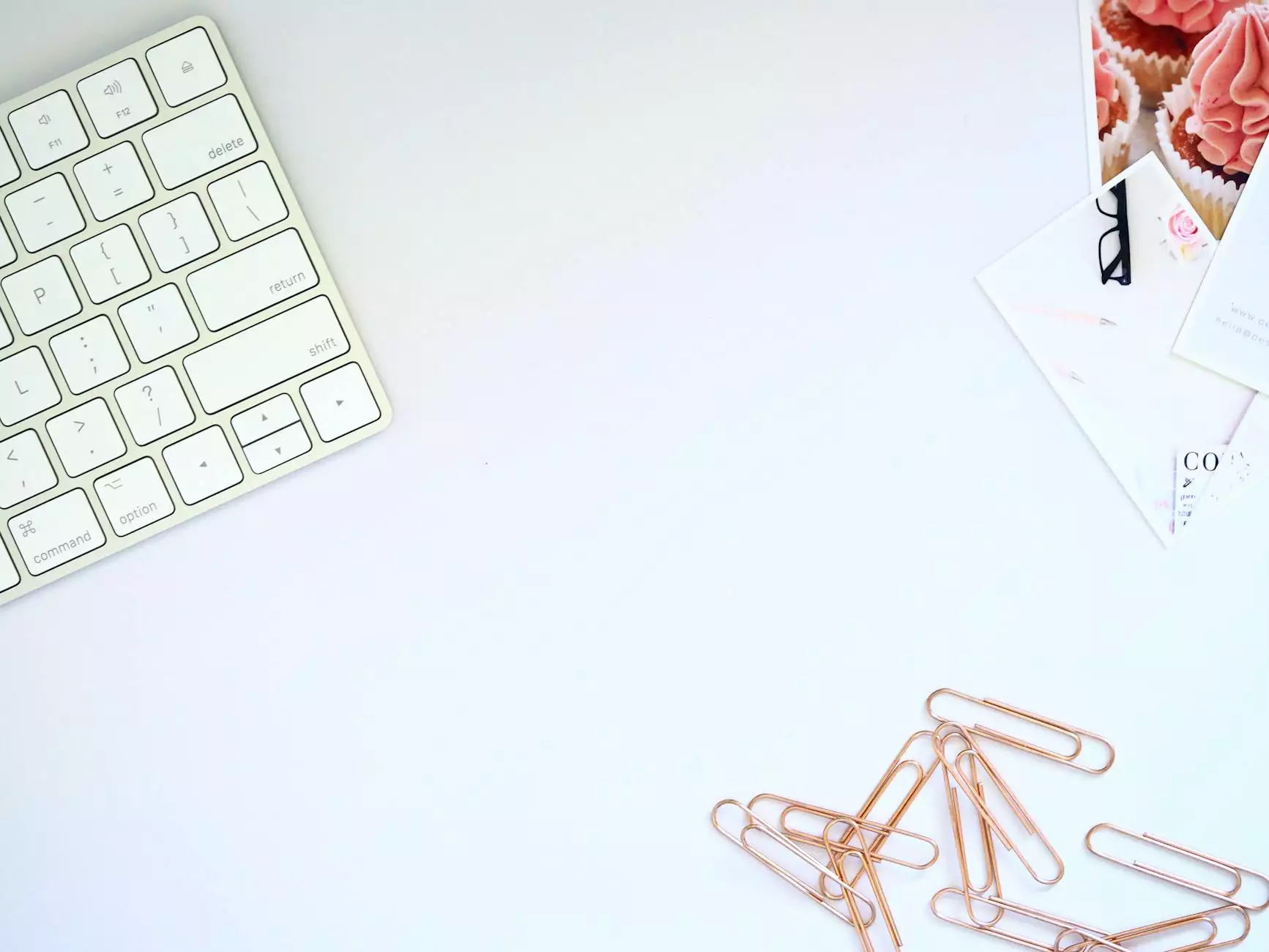
In the ever-evolving world of cutting and welding equipment, technology plays a crucial role in enhancing productivity and efficiency. One such technological innovation is represented by the term 100i. While it may initially sound like a simple alphanumeric combination, it encapsulates a wealth of information regarding modern welding solutions. This article delves deep into what 100i signifies in the context of cutting and welding equipment, its applications, and why it is vital for businesses in this industry.
The Definition of 100i in Cutting and Welding
The designation 100i often refers to a specific type of welding machine or equipment that embodies high performance and precision. Primarily, 100i can refer to:
- Current Rating: Many welding machines are rated by their amperage output; 100i denotes a 100 amp unit, effectively highlighting its capabilities in terms of depth of penetration and weld quality.
- Technical Specification: The term can also indicate particular features, specifications, or the model of a machine, emphasizing technological advancements that make the equipment versatile and efficient for various welding tasks.
Why Choosing the Right Equipment Matters
In the cutting and welding industry, selecting the appropriate equipment can make a significant difference in operational success. Here are some key reasons:
- Efficiency: Advanced machines like those marked with 100i rating offer higher efficiency rates, translating to better productivity.
- Quality of Work: Higher-rated equipment helps in achieving precise cuts and welds, which are crucial for quality assurance in projects.
- Cost-Effectiveness: With better efficiency and quality, businesses can often save significantly on costs associated with labor and material wastage.
Applications of 100i Equipment
The versatility of 100i cutting and welding equipment allows it to be utilized across various sectors, including:
- Manufacturing: Essential in the production of components, machinery, and structural elements.
- Construction: Utilized to create robust connections and frameworks in building projects.
- Automotive: Important in assembling vehicles, where precision welds are vital for safety and performance.
- Shipbuilding: Used to join materials that must withstand harsh marine conditions.
Benefits of Using 100i Equipment
Investing in 100i cutting and welding equipment comes with a multitude of benefits:
- Enhanced Performance: When you opt for high-rated equipment, you typically experience better performance metrics during operations.
- Greater Durability: Quality equipment often incorporates features that extend the lifespan, reducing replacement costs.
- Improved Safety: Advanced welding machines come with safety features that protect operators and minimize the risk of accidents.
- Ease of Use: Modern equipment is designed with user-friendly interfaces, making training and operation more straightforward.
Choosing the Right 100i Equipment for Your Needs
When selecting cutting and welding equipment labeled as 100i, consider the following factors:
- Welding Processes: Identify the processes you will use—MIG, TIG, or Stick—and ensure the equipment accommodates those methods.
- Power Supply: Ensure that the equipment aligns with your power supply options, whether it’s single-phase or three-phase.
- Portability: If you require mobility, opt for models that are lightweight and easy to transport.
- Manufacturer Reputation: Purchase from reputable suppliers, like tiendaguve.com, to ensure quality and support.
Maintenance Tips for 100i Equipment
Proper maintenance of your 100i cutting and welding machines can boost performance and longevity:
- Regular Cleaning: Keep the equipment clean from weld spatter and debris to prevent damage and maintain performance.
- Inspect Electrodes: Regularly check and replace worn electrodes to ensure consistent weld quality.
- Check Gas Connections: Ensure that gas connections are secure and functioning correctly to prevent leaks and inefficiencies.
- Follow Manufacturer Guidelines: Always adhere to the maintenance schedules and guidelines provided by the manufacturer.
Future Trends in Cutting and Welding Equipment
As technology continues to evolve, the cutting and welding equipment industry is also witnessing significant advancements. Here are some trends to watch for:
- Automation: Increasing integration of automated systems for welding processes to improve precision and reduce manual labor.
- Energy Efficiency: Innovations aimed at reducing energy consumption while enhancing output performance.
- Smart Technology: The emergence of smart machines equipped with IoT capabilities for real-time monitoring and diagnostics.
- Advanced Materials: Development of enhanced materials that require specialized cutting and welding techniques.
Conclusion
In conclusion, the designation 100i is not just a technical specification; it symbolizes advancement in the field of cutting and welding equipment. Whether you’re in manufacturing, automotive, construction, or any other industry requiring robust cutting and welding solutions, understanding and leveraging the capabilities of 100i can pave the way for improved efficiency, quality, and safety. For businesses seeking to invest in reliable cutting and welding technology, tiendaguve.com offers a range of options that incorporate the latest features to meet industry demands.
Explore More at tiendaguve.com
For more information on the latest cutting and welding equipment, including options rated at 100i, visit tiendaguve.com today to find the right solutions for your business needs.